Problems relating to external corrosion in oil and gas flowlines have historically been managed effectively, however, internal corrosion has proven to be a greater challenge. This issue is especially important, because internal corrosion is shown to be one of the main causes of pipeline failures.
Regardless of injecting a corrosion inhibitor into flowlines, oil and gas companies are seeing an increase in corrosion-related leaks. Several reasons for the cause of these leaks exist, such as low fluid velocity, greater water cut, and sulfite-reducing bacteria existing in the production streams. Oddly, even with comparable design elements, fluid composition, corrosion inhibitor amounts, and environmental situations, some flowlines experience leaks, whereas others do not.
Research was performed to determine the reason for differing corrosion rates within similar flowlines, which revealed that multiple flowline sections retained stagnant water, had a portion of the internal surface area covered by a stationary layer of solids, or both. Additionally, it was observed that some shorter flowlines with lower water cuts experienced multiple leaks, while longer flowlines with higher water cuts did not incur any leaks within the same timeframe of operation. Evaluating corrosion under sediment using corrosion models is almost impossible.
Because many onshore and offshore oil and gas facilities are nearing or reaching the end of their service lives in fields that could still prove profitable, companies are attempting to extend the useful life of their equipment. These facilities are recovering these reserves by operating at low-flow conditions. As time goes on, the necessary expenses to avoid flow-induced asset integrity problems become increasingly greater.
Unpiggable pipelines present a significant challenge, but even in piggable pipelines, pitting corrosion continues to be a major complication. The reason for this includes unwanted solids or fluids in the production stream, low-flow conditions, and the pipe wall being within a temperature range where sulfite-reducing bacteria thrive (Figure 1).
RBI models were found to have considerably underestimated the internal corrosion risk failure in numerous pipelines in which the flow was controlled by gravity. Even though the calculated probability of failure was below the target probability, the pipelines were periodically pigged, and corrosion inhibitor was continuously injected, the pipelines still experienced serious failure issues.
Downtime due to failure can lead to a major loss of revenue. In fact, the consequences of a leak in just one section of a pipeline can lead to partial or complete shutdown of an oilfield. To address this problem, researchers Yuri Fairuzov and Victor Fairuzov1 of the Multiphase Energy Corporation (Albuquerque, New Mexico, USA) predicted internal corrosion processes using ultra-high definition (UHD) simulations of four-phase and three-phase flow parameters; employed a novel technique to map adverse operational conditions; and implemented a novel flushing system to remove sediment and prevent corrosion in both piggable and unpiggable pipelines.
Identifying Areas Using UHD Simulations
Oil and gas gathering systems consist of flowlines connected to a production manifold and process facilities that move processed fluid (oil, gas, water, and solids) from wells to a main processing plant (Figure 2). Corrosion inhibitor is distributed at the wellheads. Because pigging is expensive, which is especially true when multiple pipelines are involved, it is not typically performed.
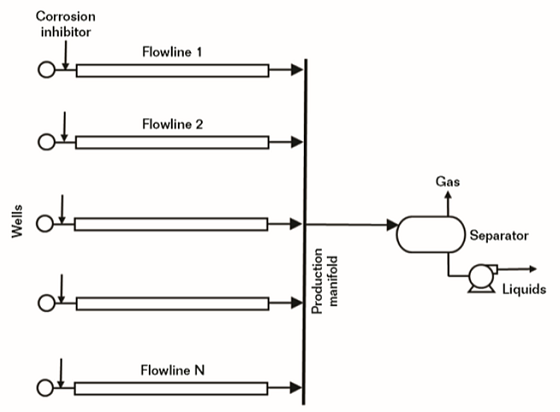
In conventional systems, inspecting for leaks via in-line inspection cannot be performed, however, an alternative approach is available. Internal corrosion direct assessment (ICDA) pinpoints areas most likely to accumulate water or water and solids. Wet gas ICDA and dry gas ICDA do not take solids transport and deposition into account in their gas-liquid flow modeling findings. Detecting the ICDA portions of the flowlines necessitates modeling and simulations of the solids transport process in three-phase flow, four-phase flow, or both, considering gas-liquid and oil-water flow patterns transpiring in the flowlines.
For this project, the researchers used a tool that produced UHD simulations of three-phase oil-water-solids flow and four-phase gas-water-solids flow, and they validated these results in multiple ways. Although leaks can ensue in any critical area, the researchers identified areas more prone to severe operating conditions. They categorized these points of failure into five categories—low, medium, medium high, high, and very high—in order to select the regions for direct examination.
The researchers conclude that it is possible for stagnant water to occur inside a flowline under certain operating conditions, and its presence can greatly increase microbiologically influenced corrosion. Additionally, when low-flow conditions are observed, solids can settle in certain portions of the flowline and form a stationary bed along the floor of the pipe, causing underdeposit corrosion. Injected chemicals cannot reach the pipe under the sediment to protect it. The bed of sediment becomes a thermal insulator that protects the sulfate-reducing bacteria along the internal wall of the pipe from high-temperature production steam.
Condition Mapping
To address the leaks experienced in similar low-flow pipelines with different corrosion rates, the researchers proposed a new technique that constructs a two-dimensional map of the adverse operational conditions. It is based on the UHD three- and four-phase flow simulations and displays the areas where problems appear.
Three operational conditions are used. Region 1, the most severe, usually forms leaks within two to three years because of exposure to both stagnant water and solids. Neither corrosion inhibitors nor biocide are beneficial, since they cannot become evenly dispersed. Region 2 tends to leak after a few years due to a stationary bed of solids. Region 3 is the most favorable operating condition, in which no stagnant water or stationary beds are formed.
The two-dimensional map produced of the unfavorable operational conditions illustrates Regions 1, 2, and 3. The researchers discovered that a shorter flowline operating at a lower water cut in Region 1 leaked multiple times, and a longer flowline operating at a higher water cut in (or close to) Region 3 had no leaks in an equivalent time period. With all other circumstances the same, it is clear the higher water cut led to a reduction in leaks for the longer flowline.
The researchers emphasize that these maps are a powerful tool to maintain pipeline integrity, but warn that a map made of a particular flowline should not be used for another similar one. One flowline, although alike, does not necessarily correspond to another due to the numerous different causes of leaks.
Novel Flushing System
Figure 3 shows a schematic of a new pipeline flushing system, a patent-pending process for removing sediment in both piggable and unpiggable pipelines. It is a pipe system that works by generating batches of liquid-containing fluid and flushing them toward the outlet—all without increasing the flow rate of transported fluids. The flow from the fluid source is never stopped throughout this process. Certain design features, such as bends, tees, welds, etc., can be problematic when attempting to clean the pipe. However, when liquid is used, as is the case in this flushing system, those limitations are removed. Furthermore, this system can remove solids in natural gas pipelines by using diesel as the liquid-containing fluid.
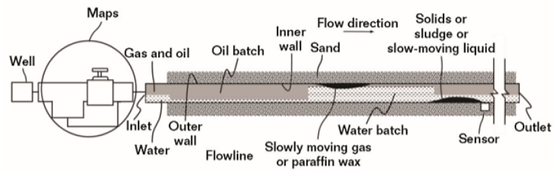
By using a scale model of the flushing system, tests show that the batches of oil and water generated by the system may reduce internal corrosion without increasing the flow rate of transported fluids.
Reference
1 Y. Fairuzov, V. Fairuzov, “Diagnosis of Internal Corrosion in Pipelines Based on Mapping Adverse Operational Conditions,” CORROSION 2019, paper no. 13250 (Houston, TX: NACE International, 2019).