Scientists at The University of Waikato (Hamilton, New Zealand) are using nanobiotechnology and solid-state fermentation to produce concrete that regenerates to repair cracks as they develop.1
The researchers are employing a bio-based injection approach to produce calcium carbonate (CaCO3) that can seal cracks from within the concrete and thus protect it over time against chloride-induced corrosion and carbonation. While concrete is inherently porous, sealing cracks delays the eventual ingress of chlorides.
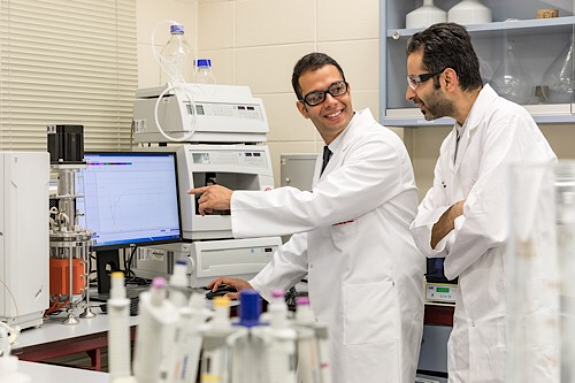
“We have engineered a process that makes [CaCO3] production very efficient, even in a harsh environment like concrete,” says Aydin Berenjian, a senior lecturer in chemical and biological engineering at the school.
Overcoming Limitations
The inherently high pH and alkalinity of concrete leads to the formation of a passive film on the surface of the steel reinforcement bars (rebar) to prevent or minimize corrosion. However, if the concrete cover protecting the steel is damaged via a crack and the bond between the concrete and rebar is broken, the steel’s passive layer can break down through carbonation or the ingress of chlorides. Carbonation results from carbon dioxide (CO2) dissolving in the concrete pore fluid. Once the passive layer breaks down, active corrosion of the steel begins. The rebar typically has a positive effect on limiting the width of cracks by controlling the shrinkage, but it does not prevent the original crack formation.
Various passive crack treatments have long been available for when cracks start to appear. For instance, the application of chemical and polymer sealers as external coating agents is one common approach, the researchers explain. But they warn that these treatments are associated with shortcomings such as poor weathering and low heat resistance, sensitivity to moisture and temperature, poor bonding with the concrete matrix, susceptibility to degradation, and delamination with age.
In recent years, the industry has increasingly focused on incorporating various self-healing agents into the concrete matrix. Upon the formation of a crack, the self-healing materials are activated and start to expand when triggered by water, moisture, or carbonation penetration—thus filling the crack.
According to Berenjian, prior studies have shown bacterially induced CaCO3 precipitation to be initially effective at filling cracks. However, the bacteria’s vulnerability to the highly alkaline and high pH levels often found in concrete, as well as the exerted shear forces on the cells during mixing and casting processes and gradual shrinkage of the concrete, eventually hurt the bacteria’s metabolic activity and its self-healing properties. As a result, Berenjian’s team sought to increase the bacteria’s stability.
New Immobilization Procedure
The team’s strategy to address the bacterial shortcomings was to protect the bacterial cells through encapsulation or immobilization prior to concrete mixing.
To accomplish this, the team turned to magnetic iron oxide nanoparticles as a protective vehicle for the bacteria. Using a coprecipitation method for nanoparticle synthesis in an aqueous medium, the magnetic characteristics of the 12- to 18-nm nanoparticles allowed them to effectively attach themselves to the bacteria. Scanning electron microscopy images showed the “efficient adsorption of nanoparticles to the Bacillus cells,” the researchers explain.
“That is where the engineering came in,” Berenjian says.
After 28 days of curing, further microscopic observation found the concrete matrix with immobilized bacteria displayed significant crack healing properties, whereas the control specimen without the immobilized bacteria did not present healing characteristics. Analysis of the generated precipitates confirmed that the minerals induced into the cracks were CaCO3.
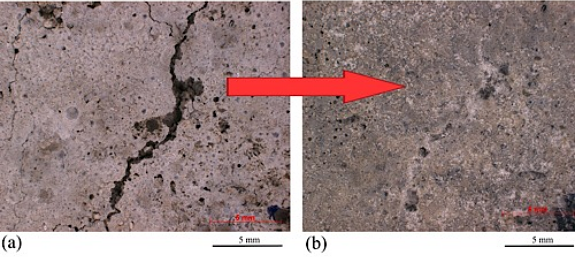
The precipitated CaCO3 crystals in bio-concrete specimens confirmed that the magnetic immobilization with iron oxide nanoparticles could successfully protect the cells from the concrete’s harsh environment without compromising the bacterial activity and biosynthesis, the researchers write. The concrete specimens supplemented with the immobilized bacteria also showed a higher resistance to water penetration. Relative to the control sample, the initial and secondary water absorption rates were 26% and 22% lower.
The bio-based, self-healing process also offers environmental benefits relative to traditional passive crack treatments, since the mechanisms to control the cracks are activated naturally and without the need for human intervention. Thus, the ecological footprint is lowered through reduced maintenance activities. The researchers believe the process has a wide range of future industry applications, including oil and gas, medicine, environmental remediation, and construction materials.
Pathway to Industrial Use
Although the researchers are optimistic about the success of the bio-concrete’s ability to self-heal due to the successful laboratory tests, they caution that several hurdles still need to be cleared before the process can be widely adopted. For example, they say the long-term efficiency and durability of the concrete with bacterially induced CaCO3 should be studied over a longer time period before industrial application.
The bacterially induced CaCO3 fabrication process is also more expensive than traditional manual crack-repair treatments. However, the researchers believe the cost issue can be mitigated if potential users consider the potential costs and resources saved in the long run.
“Fixing concrete manually also means cracks are sometimes missed, particularly if they are not visible,” Berenjian says. “The return comes with the longer-term strength.”
Source: The University of Waikato, www.waikato.ac.nz.
Reference
1 “A Revolutionary New Process for Self-Healing Concrete,” The University of Waikato News & Events, April 9, 2018, https://www.waikato.ac.nz/news-opinion/media/2018/a-revolutionary-new-process-for-self-healing-concrete (August 6, 2018).