Dew point corrosion is a well-known phenomenon in which fine water droplets condense from the vapor upon cooling, and the acid gases in the vapors diffuse into water droplets to form a highly corrosive, low-pH liquid. We have identified a similar mechanism in hydrocarbon liquids (HLs), which we call “Nucleation Corrosion.” HLs leaving warm separators are saturated with dissolved water (DW). Upon cooling, the DW nucleates as sub-micron free water drop-lets and acids present in the HL partition into the water droplets, causing aggressive corrosion, called nucleation corrosion. Evidence supporting this mechanism, mitigation strategies, and a field case are presented here.
The condensation of acidic species from vapor to liquid occurs when the system is cooled to or below the dew point temperature.1-2 Such condensation leads to extremely aggressive corrosion that is referred to as acid dew point corrosion. Some also refer to this corrosion as low temperature corrosion or cold corrosion. Dew point corrosion is common across various industries.
One widely reported example is sulfuric acid (H2SO4) corrosion in flue gas systems.1-2 Sulfur oxide (SO2) is often the dominant acid gas formed by combustion of sulfur-containing fuel. At the dew point, sulfur oxide in vapor condenses to sulfuric acid in the liquid phase, which is an extremely corrosive acid. Another well-known example in refineries is the hydrochloric acid (HCI) corrosion in crude unit distillation overheads.3-4 Calcium and magnesium chloride (MgCl2) salts that are carried with the crude oil hydrolyze in crude heaters to produce HCl. The volatile HCl is carried to the overhead of the distillation unit where it condenses at the dew point, resulting in extremely low pH droplets causing aggressive corrosion.
In this study, we report a low-temperature corrosion mechanism that is like dew point corrosion, except it occurs in hydrocarbon liquids. Hydrocarbon liquids that leave warm separators such as in oilfield or distillation unit overhead accumulators are saturated with dissolved water (DW). After leaving the separator, the temperature of these liquid streams drops, resulting in supersaturated water that nucleates as fine water droplets.5–8 Acidic species such as hydrogen sulfide (H2S) and short chain organic acids9 like formic and acetic acids diffuse into these droplets, lowering the pH of the microdroplets, which causes aggressive corrosion. This mechanism has been termed here as nucleation corrosion as it is primarily driven by nucleation of DW in liquid hydrocarbons.10 A series of experiments is presented to demonstrate the concept of nucleation corrosion in the oil phase; impact of various corrosive species including organic acids and H2S on nucleation corrosion; and strategies to mitigate nucleation corrosion including a real-world situation involving naphtha reflux line.
The Mechanism
The corrosion in liquid hydrocarbon systems is tied to the presence of free and/or emulsified water in hydrocarbon liquids and the corrosive species therein. Little attention is paid to the DW content of oils. DW is always present in hydrocarbon liquids leaving two-phase or three-phase separators/contactors. Such vessels are ubiquitous in oil fields, midstream operations, refineries, and even petrochemical plants. Sufficiently long residence time drives the DW con-tent to near saturation levels, which can range from 10s of parts per millions (ppm) to several percentage points, depending on the oil composition and temperature.11 In this dissolved state, water is not available as a free water phase; hence, it does not promote acidic, pH-driven corrosion. However, the water-saturated oil often cools in pipelines downstream of the separators/contactors, resulting in reduced water solubility and leading to nucleation of free water microdroplets (Figure 1).10 Acidic species diffuse into the droplets, dropping the pH to cause Nucleation Corrosion.
Corrosion Experiments
Weight loss
In a demonstration (Figure 2), two bottles containing naphtha with 100 ppm ace-tic acid were saturated overnight with excess water at 60 °C (140 °F) (HOT). Car-bon steel (CS) coupons were then introduced in both bottles while the samples were still hot. One of the bottles was maintained at 60 °C, and the other bottle was allowed to cool to ambient temperature (COLD). The bottle at ambient temperature started corroding within a few min-minutes, whereas little corrosion was observed in the bottle held at 60 °C.10 The weight-loss data and the corresponding coupons show a stark difference in the corrosion rate (COLD = 25 mpy vs. HOT = 2 mpy) due to cold nucleation corrosion. When the experiment was repeated with the same fluids, temperatures, and procedure, but without acetic acid, corrosion in both HOT and COLD samples was low (<1 mpy).
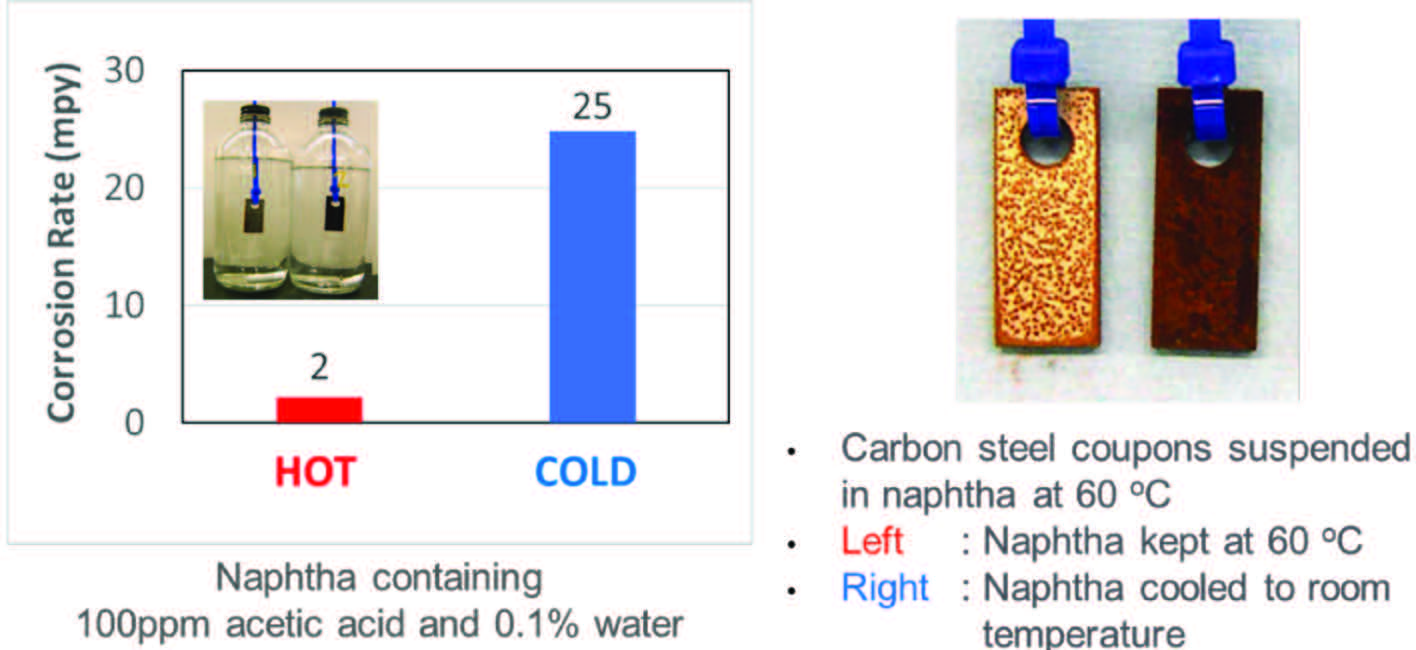
Measuring pH
The diffusion of acetic acid into the sub-micron droplets causes the droplets to become acidic and corrosive. Since the amount of water that precipitates is extremely small (10s to 100s of ppm), a pH probe could not be used to validate the acidic pH. Instead, several liters of naphtha with 100 ppm acetic acid were equilibrated with 300 ppm of water that was completely soluble at 60 °C. This naphtha sample upon cooling at 5 °C (41 °F) presented visible water droplets stuck to the bottom of the jar (Figure 3). A pH paper was first immersed in the naphtha phase to confirm that there was no change in color. A second pH paper was then dropped into the jar so that it would read the pH of the nucleated water. A pH of ~3.3 was registered, confirming that the pH was in the corrosive range due to partitioning of acetic acid into water nuclei. The pH of the initial nuclei that precipitated at 20 °C (68 °F) was likely more acidic than pH ~3.3 as the droplets became more diluted with additional water that precipitated upon cooling to 5 °C.
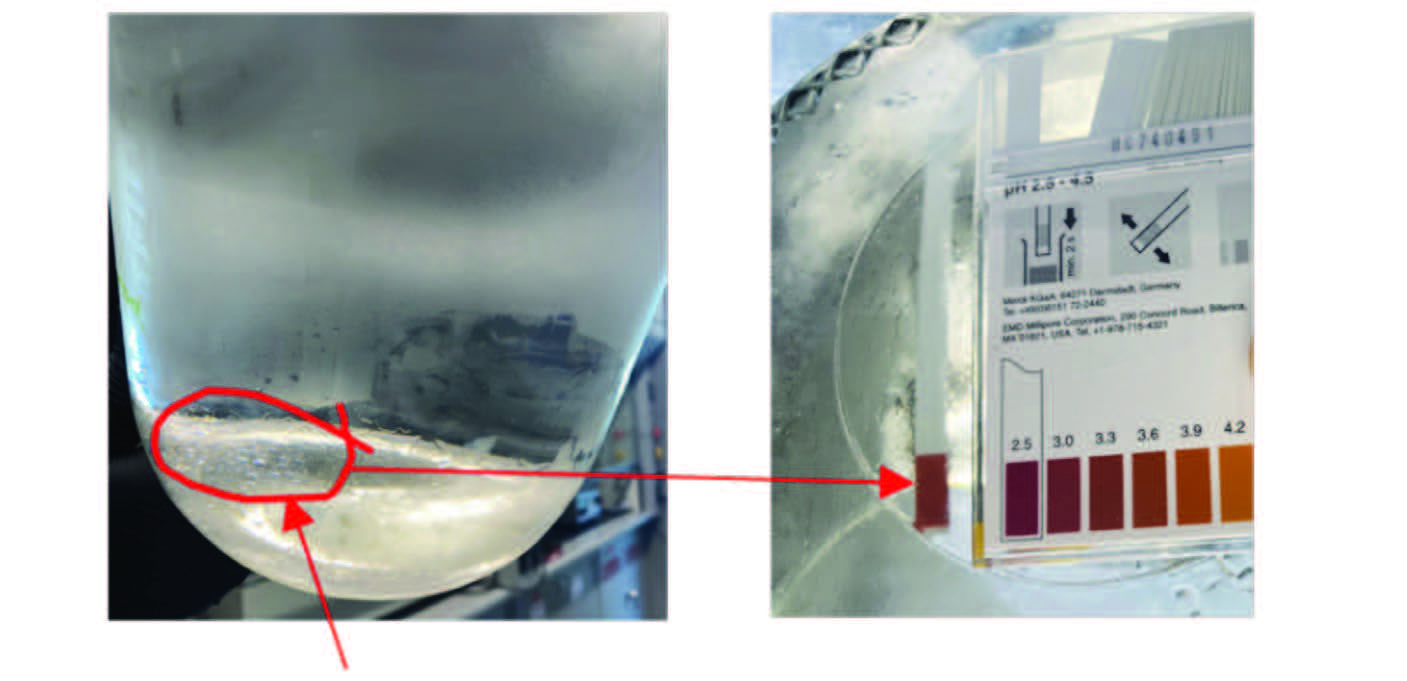
Corrosive Species–Impact of Concentration, Type of Organic Acids, and H2S
Concentration of acetic acid. Sensitivity of acetic acid concentration to nucleation corrosion was tested by varying the acid concentration from 0 to 50 ppm. All the test conditions were like the naphtha case described earlier.10 A clear dose-dependent corrosion trend was observed, with the corrosion rate varying from <2 mpy at 5 ppm acetic acid, to 3, 16, and 19 mpy at 10, 25, and 50 ppm acetic acid, respectively. This indicated that a threshold concentration of 10 ppm acetic acid was needed in this fluid and test conditions for a significant amount of acid to partition to the nucleated water.
Impact of varying organic acid types. To study the impact of the type of organic acids, four homologous series of acids were tested: (i) formic acid, (ii) acetic acid, (iii) propionic acid, and (iv) butyric acid, at equimolar acid concentration corresponding to 100 ppm acetic acid (Figure 4, top). Both formic and acetic acid resulted in high corrosion rates (14 and 17 mpy, respectively), whereas the propionic and butyric acid corrosion rate was equivalent to the control sample without acid (2 mpy). This was somewhat expected, as the longer organic acids (C3 and C4) have a lower partition coefficient to water,9 especially at low pH as is the case with nucleated water that has no buffer. This distribution was confirmed by extracting the oil with water and quantifying the organic acids (Figure 4, top).
With H2S as corrosive species. It is not uncommon for hydrocarbon liquids to have measurable concentrations of acid gases, including H2S. To evaluate the impact of H2S on water nucleation corrosion, synthetic naphtha was sparged with 5% H2S to about 10 ppm H2S in the liquid phase.10 As with the acetic acid experiment, H2S-laden naphtha was saturated with water in the oven. One of the bottles was maintained warm, whereas the other bottle was removed to ambient temperature. After aging for three days, the measured corrosion rate with the ambient (cooler) sample was 25 mpy vs. 5 mpy for the warm sample (Figure 4, bottom). The SEM-EDS analysis of the corrosion products (Figure 4, bottom) shows iron sulfide to be the dominant corrosion species, confirming H2S-driven corrosion. The ~5-fold increase in corrosion rate upon cooling supports the idea that H2S partitioned to the water nuclei to enhance corrosion.
Impact of Hydrocarbon Composition
Hydrocarbon composition can impact nucleation corrosion in a couple of different ways. To study the first path, temperature- driven acetic acid nucleation corrosion was conducted in oils with different compositions: 1) naphtha, which is a mix of aliphatic, isoparaffinic, cycloparaf finic, and aromatic compounds, and 2) heptane that has aliphatic character only. The corrosion in heptane was lower overall compared to synthetic naphtha (10 vs. 25 mpy).10 A couple of factors could be influencing this behavior. Based on composition, naphtha dissolves more water with an increase in temperature compared to aliphatic solvents.5–8 Hence, this would encourage a larger volume of water nucleation upon cooling, which would facilitate better acetic acid transfer for corrosion. The partitioning difference of acetic acid in heptane water vs. naphtha water could also impact the behavior.
In the second, not-so-obvious path, a change in hydrocarbon composition without temperature drop could trigger nucleation corrosion. In one example, blending water-saturated, aromatic-rich oil with a paraffin-rich oil could reduce water solubility just due to the composition change. In another case, flashing of light ends (e.g., in flash drums, stabilizers) changes the composition of the bottoms’ liquid enough to decrease solubility of water, which can result in water nucleation. Lastly, a change in pressure across compressors can change the density/character of the natural gas sufficiently to trigger a reduction in water solubility.14 In all cases, corrosive species in hydrocarbon oil can partition to the nucleated water to cause corrosion.
Mitigation of Nucleation Corrosion
Mitigating corrosion by process changes is always desirable, if possible. For example, nucleation corrosion could be mitigated by reducing temperature changes as is sometimes done in chemical processes and refineries. Similarly, reducing the DW content to below the solubility limit at the coldest location of the pipeline would prevent nucleation. Finally, the elimination of corrosive chemical species that preferentially partition to nucleated micro-droplets would also reduce the risk of nucleation corrosion. However, these options require substantial revision to pipeline tariff specifications and/or significant modifications to pipeline design, neither of which is practical for existing pipelines.
The key aspect required to ensure the effectiveness of an inhibitor is to choose an inhibitor that is available in the oil phase when the droplets are formed. It is often believed that water-based inhibitors should be preferred due to their partition to water phase, where corrosion occurs.13 However, for nucleation corrosion, the inhibitor first needs to be present in the oil and partition to the water droplets when they precipitate. Due to the nature of the nucleation corrosion mechanism, the test method also plays a crucial role in identifying an effective inhibitor. Traditional procedures followed for rotating cylinder electrode testing may need to be revisited to mimic the mechanism described here.15
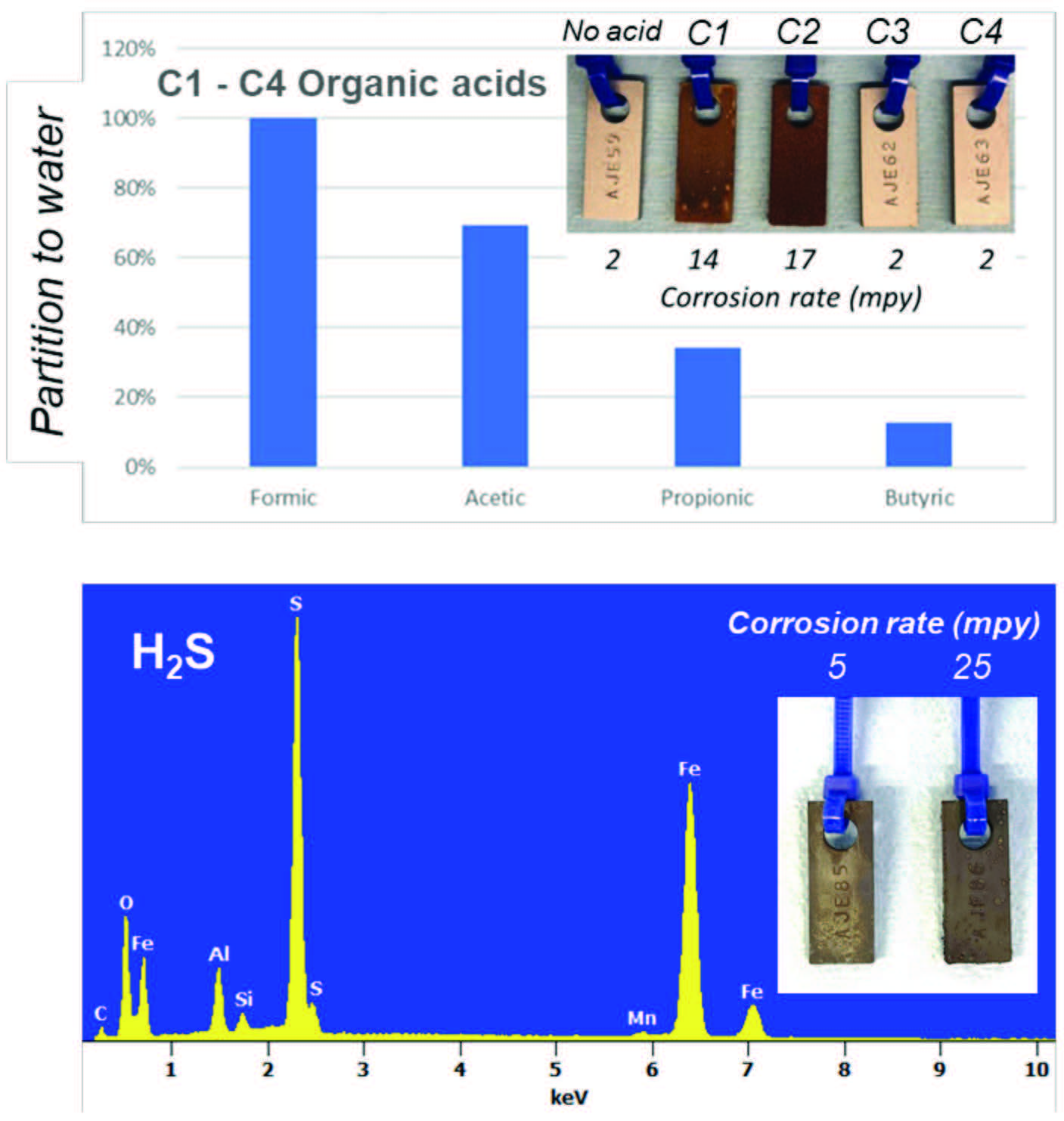
Case Study: Nucleation Corrosion in Distillation Overhead Reflux
A refinery gasoline splitter unit was experiencing corrosion in the overhead system. The corrosion in the vapor phase and condensing system was due to the well-known dew point corrosion. This corrosion issue was controlled by thoroughly analyzing the system and injecting suitable overhead neutralizer and inhibitor chemistries. However, there was still an unexplainable corrosion in the naphtha reflux line, which did not have free water, as it was already separated in the accumulator. Detailed analysis of naphtha showed high levels of organic acid. The field naphtha containing 3 ppm, 106 ppm, 6 ppm, and 124 ppm of formic, acetic, propionic, and butyric acid, respectively, was subjected to a nucleation corrosion test like that described in Figure 2. The sample that was kept warm (50 °C [122 °F]) maintained a low corrosion rate of <2 mpy. However, the reflux naphtha sample that was brought to ambient temperature started showing corrosion within minutes and gave a corrosion rate of 17 mpy at the end of the test. Field inspection confirmed a significant portion of the reflux circuit was not insulated, which is suspected of causing heat loss and a drop in temperature, leading to nucleation corrosion. Insulation was proposed as a long-term engineering solution to this problem. An immediate proposed fix was injection of an effective neutralizer in crude oil to control organic acid in the overhead, as well as using the oil-soluble inhibitor that was available in the reflux naphtha.
Conclusions
A series of controlled experiments was carried out to investigate the mechanisms of nucleation corrosion in hydrocarbon liquids. This is relevant to production, processing, transportation, and refining of various hydrocarbon liquids, as these systems involve the presence of water, acidic species, and significant variation in composition and temperature.
Simple bottle tests clearly demonstrated an aggressive increase in corrosion rate due to nucleation corrosion, when the temperature of water-saturated synthetic naphtha containing acetic acid was dropped from 60 °C to ambient temperature. A similar increase in corrosion upon temperature reduction was also observed with H2S in water-saturated naphtha. It was also demonstrated that longer-chain organic acids, such as propionic and butyric acids, which are more soluble in liquid hydrocarbon, do not cause significant corrosion due to poor partitioning to water phase upon nucleation of water.
Hydrocarbon composition was shown to have a significant impact on nucleation corrosion. A change in composition from aromatic (e.g., naphtha) to paraffinic (e.g., heptane) oil resulted in decreased corrosion due to lower solubility of water in paraffinic oil. Water nucleation related to hydrocarbon composition is expected to occur in various units that flashlight ends or compress natural gas that cause water supersaturation and shedding.
A real-world example involving the ref lux line of a naphtha splitter was described, where high levels of organic acids were shown to cause nucleation corrosion. These findings provided useful insights to develop methods, such as proper insulation or use of effective corrosion inhibitors, to mitigate nucleation corrosion.
Acknowledgements
The authors would like to acknowledge (1) analytical testing support provided by Customer Analytical Services Laboratory of Veolia Water Technologies & Solutions (VWTS) facility in Tomball, Texas, USA, and (2) product application subject matter experts of VWTS for valuable discussions about their field experience in the context of nucleation corrosion. The authors would especially like to thank Mel Esmacher and Tatiana Barbosa for their support.
Disclaimer: Any information or data pertaining to Enbridge Employee Services Canada Inc., or its affiliates, contained in this paper was provided to the authors with the express permission of Enbridge Employee Services Canada Inc., or its affiliates. However, this paper is the work and opinion of the authors and is not to be interpreted as Enbridge Employee Services Canada Inc., or its affiliates,’ position or procedure regarding matters referred to in this paper. Enbridge Employee Services Canada Inc. and its affiliates and their respective employees, officers, director, and agents shall not be liable for any claims for loss, damage or costs, of any kind whatsoever, arising from the errors, inaccuracies or incompleteness of the information and data contained in this paper or for any loss, damage or costs that may arise from the use or interpretation of this paper.
References
1 W. Zuo, X. Zhang, Y. Li, “Review of Flue Gas Acid Dew-Point and Related Low Temperature Corrosion,” J. of the Energy Institute 93, 4 (2020): pp. 1,666–1,677.
2 W. Huijbregts, R. Leferink, “Latest Advances in the Understanding of Acid Dewpoint Corrosion: Corrosion and Stress Corrosion Cracking in Combustion Gas Condensates,” Anti-Corrosion Methods and Materials 51, 3 (2004): pp. 173–188.
3 NACE Publication 34109-2009-SG, “Crude Distillation Unit—Distillation Tower Overhead System Corrosion” (Houston, TX: NACE International, 2009).
4 B. Chambers, et al., “Corrosion in Crude Distillation Unit Overhead Operations: a Comprehensive Review,” CORROSION 2011, paper no. 11360 (Houston, TX: NACE, 2011).
5 C. Tsonopoulos, G.M. Wilson, “High-Temperature Mutual Solubilities of Hydrocarbons and Water Part I: Benzene, Cyclohexane, and n-hexane,” AICHE J. 29, 6 (1983): pp. 990–999.
6 J. Heidman, et al., “High-Temperature Mutual Solubilities of Hydrocarbons and Water Part 2,” AICHE J. 31, 3 (1985): pp. 376–384.
7 C. Tsonopoulos, “Thermodynamic Analysis of the Mutual Solubilities of Normal Alkanes and Water,” Fluid Phase Equilibria 156, 1-2 (1999): pp. 21–33.
8 A. Groysman, Corrosion in Systems for Storage and Transportation of Petroleum Products and Biofuels: Identification, Monitoring and Solutions (Berlin, Germany: Springer Science & Business Media, 2014).
9 M.A. Reinsel, J.J. Borkowski, J.T. Sears, “Partition Coefficients for Acetic, Propionic, and Butyric Acids in a Crude Oil/Water System,” J. Chem. Eng. Data 39, 3 (1994): pp. 513–16.
10 H. Bagaria, et al., “Nucleation Corrosion in Liquid Hydrocarbons,” CORROSION 2023, paper no. 19463 (Houston: TX: AMPP, 2023).
11 Gas Processing Suppliers Association Engineering Data Handbook, 14th ed. (Tulsa, OK: 2017).
12 B.J. Berne, R. Pecora, Dynamic Light Scattering: With Applications to Chemistry, Biology, and Physics (North Chelmsford, MA: Courier Corporation, 2000).
13 R.C. Woollam, S.J. Merrett, “Why Water Soluble Corrosion Inhibitors Should be the Preferred Choice for Continuous Applications,” SPE Western Regional Meeting, paper no. SPE-27869-MS (1994).
14 A. Chapoy, et al., “Estimation of Water Content for Methane+ Water and Methane+ Ethane+n-Butane+ Water Systems Using a New Sampling Device,” J. Chem. Eng. Data 14, 50 (2005): pp. 1,157–1,161.
15 M. Adewale, et al., “Inhibiting Nucleation Corrosion in Liquid Hydrocarbons,” CORROSION 2024, paper no. 21232 (New Orleans, LA: AMPP, 2024).
HITESH BAGARIA is advanced R&D manager for Veolia Water Technologies & Solutions, Tomball, Texas, USA, email: hitesh.bagaria@veolia.com. He has 10-plus years of experience in developing solutions for the hydrocarbon processing industry with a focus on corrosion, flow assurance, phase separation, and fuel additives. He has a Ph.D. in chemical engineering from the University of Alabama, 30-plus peer-reviewed publications, and 10 patents. He has been a member of AMPP for three years.
MOSHOOD ADEWALE is associate researcher for Veolia Water Technologies & Solutions, email: moshood.adewale@veolia.com. His primary focus is on asset integrity, flow assurance for hydrocarbon production, and mitigating H2S challenges within the oil production and refining processes. He is a co-inventor on three patents/patent applications in the areas of flow assurance and H2S mitigation.
NIMESHKUMAR PATEL is senior R&D manager researcher for Veolia Water Technologies & Solutions, email: nimeshkumar.patel@veolia.com. He focuses on the commercialization of innovative chemical and monitoring solutions to address asset protection, phase separation, and flow assurance for hydrocarbon and petrochemical production and processing challenges as well as the commercialization of innovative chemical and monitoring solutions to address asset protection, phase separation, and flow assurance for hydrocarbon and petrochemical production and processing challenges.
JENNIFER SARGENT is national account manager for Veolia Water Technologies & Solutions, Edmonton, Alberta, Canada, email: jennifer.sargent@veolia.com. She has been a member of AMPP for eight years.
TREVOR PLACE is senior specialist for Enbridge Inc., Edmonton, Alberta, Canada,email: trevor.place@enbridge.com. He has 34 years of professional practice with a specialty in internal corrosion management and cathodic protection. He has been a member of AMPP for 32 years.