Improving fired heater performance is crucial for optimizing energy consumption, reducing emissions, and enhancing overall process performance. In large-scale process facilities, energy typically accounts for at least 50% of operating costs. An energy use reduction of 10% will often improve margins by 5% and reduce CO2 emissions by 10%.
This article will discuss symptoms and causes of fired heater performance issues, and the solutions available to fix them and improve efficiency.
What are the Symptoms of Underperforming Fired Heaters?
Inefficient fired heaters can lead to increased energy consumption, decreased production rates, and potentially unsafe operating conditions. There are several symptoms of fired heater underperformance:
- Elevated bridgewall temperature
- Tube overheating
- High stack temperature
- Production bottleneck
- Excessive CO2 and NOx emissions
- Insufficient process pre-heat/steam production
- Excessive ammonia slip
What are the Causes and Solutions of Underperforming Fired Heaters?
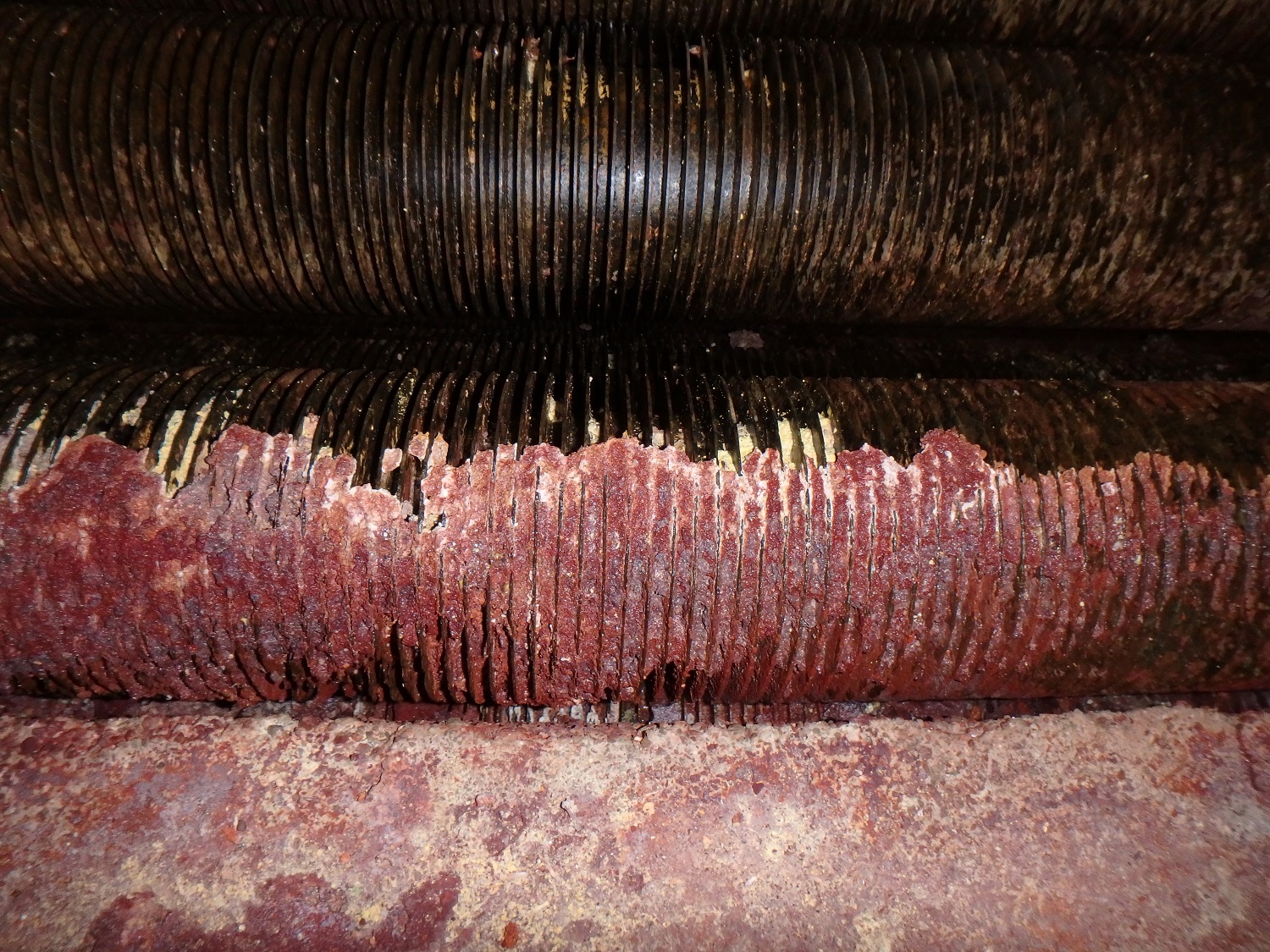
Cause 1: Fouled Convection Section Tubes
Fouling, which is the accumulation of deposits on the inner surfaces of the heater tubes in the convection section, can reduce heat transfer efficiency. Common fouling agents include carbon deposits, coke, ash, and other particulates. Fouled tubes can reduce heat transfer rates, increase fuel consumption, and decrease overall efficiency.
Solution 1: Robotic Convection Section Cleaning
To restore heat transfer efficiency, convection section tubes should be cleaned regularly. Robotic methods to remove fouling are now favoured as they offer several benefits compared to traditional manual cleaning methods, including:

Increased efficiency and speed: Robotic systems are more precise and can navigate complex geometries and hard-to-access areas with greater speed. This results in faster cleaning cycles and reduced downtime during maintenance.
Remote Operation: Robotic cleaning systems are often operated remotely, allowing technicians to control and monitor the cleaning process from a safe distance. This is particularly advantageous in situations where the convection section poses safety challenges.
Cost Saving: The initial investment in robotic cleaning services can often be higher than manual labor costs, however, the long-term benefits often outweigh this. Improved efficiency, reduced downtime, enhanced performance, and decreased maintenance needs can lead to significant cost savings over the equipment's lifespan.
Environmental Benefits: Efficient convection section cleaning helps maintain optimal heat transfer efficiency, leading to reduced energy consumption and lower CO2 and NOx emissions. This aligns with sustainability goals and environmental regulations.
Conducting a technical evaluation before cleaning the convection section is advisable. This will indicate the expected performance gains in terms of an increase in capacity, a percentage reduction in emissions, and fuel consumption benefits.
Watch: Robotic Convection Cleaning
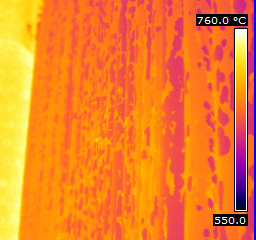
Cause 2: Radiant Tube Scaling
Radiant tubes are designed to transfer heat from the combustion of fuel to the process fluid or material being heated. However, they are susceptible to scaling, which is the deposition of solid materials on the external surfaces of the tubes. Scaling can have several negative effects on the performance and efficiency of radiant tubes including reduced heat transfer efficiency, tube overheating, emissions increase, and higher bridgewall temperatures.
Solution 2: High Emissivity Coatings
High emissivity coatings, such as Cetek coatings, are materials that besides improving radiant heat transfer, also prevent oxidation and scale formation on the radiant tubes. These coatings are applied to the external surfaces of the tubes and significantly enhance heat transfer to the process and protect tubes from scaling. They are designed to withstand high temperatures and harsh operating conditions.

Some of the benefits of high emissivity coatings include:
Extended Tube Lifespan: By preventing oxidation and associated tube wall thinning, the life of the radiant tubes can be extended, if oxidation is the limiting factor.
Reduced Fuel Consumption: High emissivity coatings can help achieve the desired process temperatures with less energy input by improving heat transfer efficiency. This can lead to reduced fuel consumption and lower operating costs.
Watch: Catalytic Reformer Heater Process Tube Coating

Cause 3: Refractory Deterioration
Refractory deterioration can lead to hot spots on refractory material. It is an area of localized high temperature within a furnace, kiln, or other high-temperature process equipment where the refractory material is exposed to more intense heat than the surrounding areas. Hot spots can occur for various reasons and can have negative implications for the performance, efficiency, and lifespan of the refractory lining.
In these cases, the operator must decide whether to interrupt production by bringing the heater off-line to make a conventional repair or continue at reduced capacity until the next scheduled shutdown.
Solution 3: Online Heater Repairs
To avoid costly shutdowns or operating at a reduced capacity, it is possible to conduct online refractory repairs until further maintenance can take place during a planned shutdown.
Online refractory repair can be a valuable strategy to extend the lifespan of refractory linings and minimize downtime. However, it should only be performed by qualified and experienced personnel following proper safety guidelines and in accordance with industry best practices. Consulting with Hot-tek refractory experts and conducting thorough assessments are essential to ensure a successful outcome.
See How it Works: Online Refractory Repair
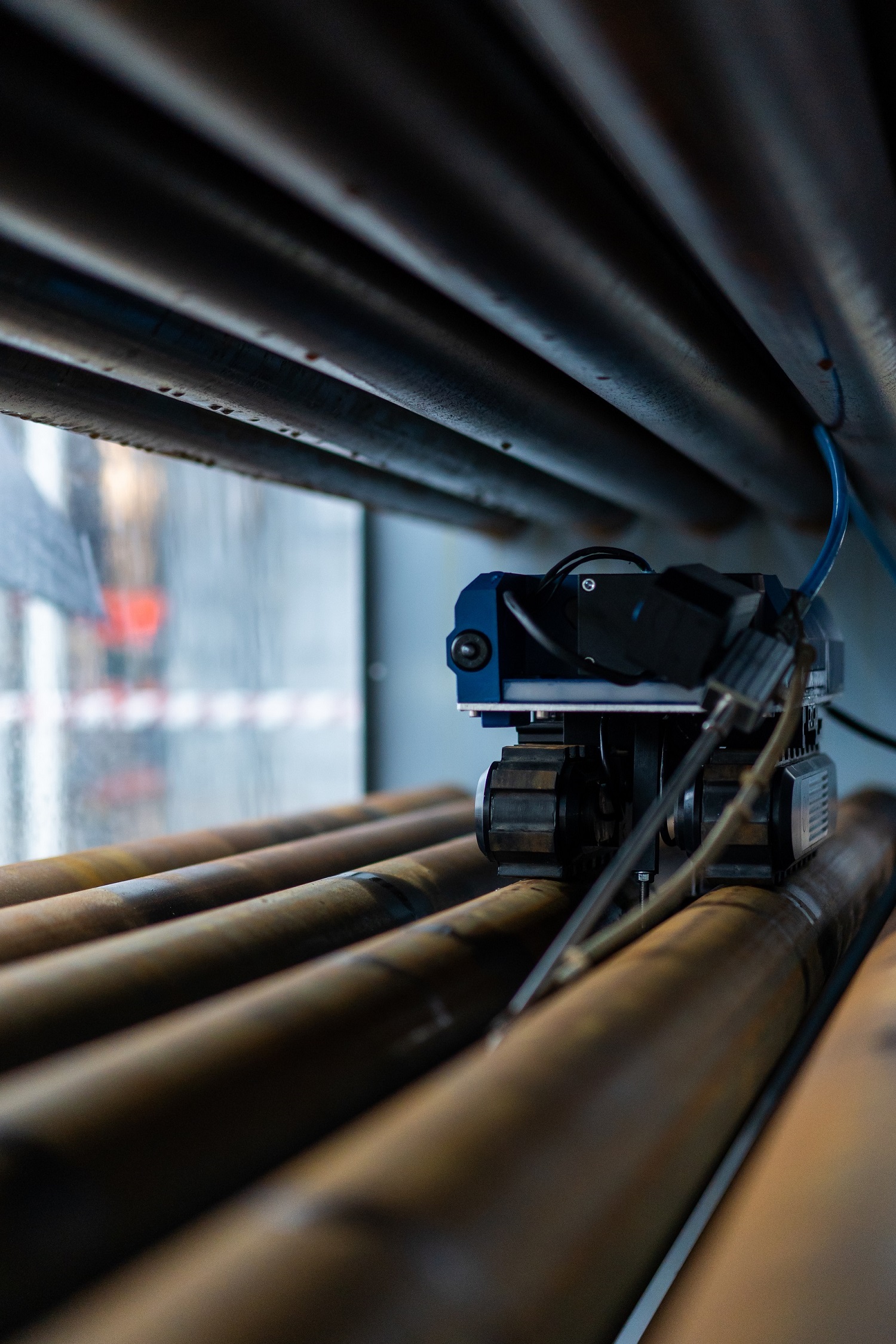
Conclusion
There are many causes of fired heater underperformance. It is important to identify warning signs early as even a 1-2% decrease in efficiency in fired heaters can consume an additional $1M in fuel across a 12-month period.
To address this issue, it's crucial to conduct regular inspections, implement proper maintenance practices, monitor operating parameters, and address any issues promptly. Engaging with experienced process engineers and fired heater experts can help diagnose and resolve underperformance issues effectively.
Contact Integrated Global Services (IGS) for a free technical evaluation.
IGS fired heater experts will perform a comprehensive technical evaluation that will determine your efficiency improvement (%) and the payback period, as well as projected (%) improvement based on your objectives (fuel/emission reduction, capacity increase or a combination of both).
To claim your free technical evaluation, visit: www.integratedglobal.com.