Vapor phase corrosion inhibitors (VCIs) are a well-known and highly versatile range of products for the prevention of corrosion.1 VCIs can be delivered to the target metal in a variety of ways. One common product is plastic packaging.2 Plastic VCI films are a versatile and highly effective article for protection of items from corrosion. They are generally made from polyethylene (PE), which is readily available, cost effective, and usually recyclable.3 Production of VCI films usually results in the production of at least some “scrap” film. This may be film of variable size produced during production start-up, or film that does not meet specifications. Scrap can be disposed of as trash, but is preferably recycled. The usual mode of recycling is to reprocess it (melt processing) into pellets that can be reused in production of new film.3 It is often referred to as “repro.” Reprocessing can be done in-house with dedicated machines or the scrap can be sent to external facilities that specialize in recycling. The quality of repro can vary considerably with the quality/purity of the scrap and the conditions used for reprocessing (particularly temperature and shear).4 In this article, studies are cited on varying the source and quantity of repro and the effects on product quality. Results and commercial implications are discussed.
Experimental Procedures
Materials
Plastic Resins
Commercial low-density PE (LDPE) and linear low-density PE (LLDPE) were used in proprietary combinations for the production of films. Slip and anti-block additives were used as necessary.
VCIs
VCIs were composed of proprietary formulations. The VCIs were added to the pellet blend as a master batch.
Reprocessed Plastic Resins
In-house reprocessed resin (repro) was prepared from VCI film scrap at two different facilities, using commercial re-granulator equipment. Some experiments utilized a commercial repro of LDPE. This was a clear material with a melt index of ~2 (2.16 kg, 190 °C). Sources varied.
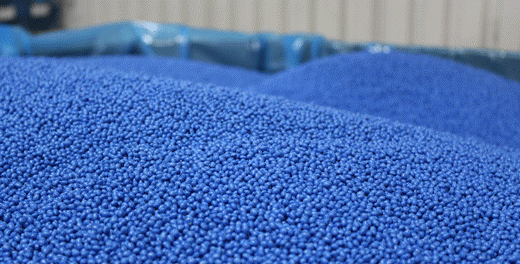
Methods
Monolayer Blown Film Extrusion
Films were produced on commercial blown film production lines in Cambridge, Minnesota, using standard melt processing temperatures in the range of 160 to 200 °C. Films contained a blend of commercial film-grade PE resins (LDPE and/or LLDPE). All samples contained a proprietary VCI, added as a master batch. Total concentration of active ingredients in the final film was ~2% by weight.
Coextruded Blown Film Extrusion
Films were produced on commercial blown film production lines in Beli Manastir, Croatia, using standard melt processing temperatures in the range of 160 to 200 °C. Films contained a blend of commercial film-grade PE resins (LDPE and/or LLDPE). All samples contained a proprietary VCI, added as a master batch. Total concentration of active ingredients in the final film was ~1-2% by weight, depending on the specific film construction. The coextrusion die produced three layers (fed by three separate extruders).The general film construction included thickness/wt% of 25/50/25 for the three layers, respectively. VCI was added to one or more of the layers depending on the specific product.
Physical Property Testing
The physical property testing was conducted with commercial testing instrumentation per the methods referenced below. These are primarily methods from ASTM for determining film thickness (caliper), ASTM D6988;5 tensile properties, ASTM D882-02;6 impact, ASTM D1709-04 Method A;7 tear, ASTM D1922-06A;8 coefficient of friction, ASTM D1894;9 and seal strength, ASTM F88-99.10
Puncture resistance was determined according to Test Method 2065 of Military Standard 3010.11 The results are generally shown with the number of digits in the instrument output report. However, for comparison purposes, differences between film sample results of less than about 10% are not considered significant. While the test methods can be quite precise, there is considerable variability in film samples due to small differences in composition and the effects of processing variables. In particular, physical properties of blown films are strongly dependent on orientation of the molecules in the film, which is a complex function of molecular structure, bulk melt viscosity/elasticity, processing temperatures, equipment design, cooling rate, processing speed, and blow up ratio (ratio of bubble diameter to die diameter).12 Many material properties are measured in both the machine direction (MD) and transverse direction (TD), as these properties are often different due to the different extent of orientation in these directions. For some properties, it is common for the MD and TD to be inversely correlated (as one increases, the other decreases).
Vapor-Inhibiting Ability Corrosion Inhibition Test
The vapor-inhibiting ability (VIA) test measures the effectiveness of the VCI. Testing was performed by standard methods as previously described.13 In brief; sanded carbon steel (CS) plugs are suspended from a modified lid in a quart jar. Strips of the test substrate, 1 by 6 in (25 by 150 mm) are hung from the inside of the lid, ensuring they do not come in contact with the plug. The jars are left to condition for 20 h at ambient temperature. After conditioning, a glycerol/water solution is added to the jars to accelerate corrosion and left to sit at ambient temperature for 2 h, then in a 40 °C oven for 2 h. The plugs are removed and rated on a scale of 0 (heavily corroded) to 3 (no visible corrosion). A grade of 2 or 3 is considered passing.
Razor Blade Corrosion Inhibition Test
This test measures the effectiveness of the film in preventing corrosion when in direct contact with a metal surface. Testing was performed by standard methods as previously described.13 In brief, CS panels are cleaned in methanol and dried. Two drops of deionized (DI) water are placed on the metal panel and covered with the substrate of interest. After 2 h, the substrate is removed and the panels are inspected. Panels with any sign of corrosion, pitting, or staining are deemed to “fail” the test. A second test is conducted with copper panels. The method is the same except that a 0.005% (by weight) sodium chloride (NaCl) solution is used instead of water and the test time is extended to 4 h.
Results
Monolayer Films
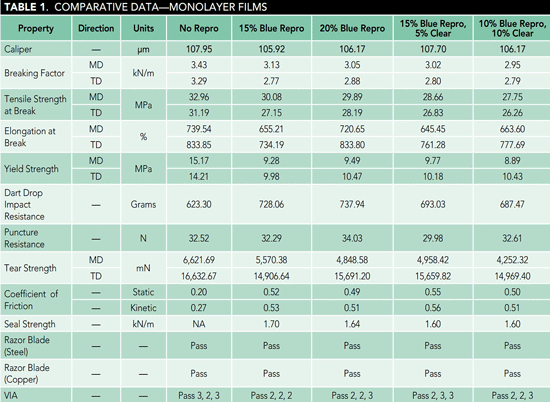
The films compared in Table 1 were produced on a machine with an 8-in (200-mm) diameter die, with a blow up ratio of 2:1. The “blue repro” is material made in-house from VCI scrap. The “clear repro” is commercially purchased material containing no VCI. The table shows a comparison of films containing up to 20% repro (in various combinations) with a comparable formulation containing all virgin resins (no repro).
All of the samples passed the corrosion inhibitor tests. Most of the physical property results are not considered to be significantly different. The differences in the coefficient of friction values are due to different levels of slip and anti-block additives in the formulations (not to the use of repro). There are possibly real differences between samples for yield strength, tear strength, and tensile strength at break, with the repro containing formulations showing slightly reduced properties. However, all films are perfectly acceptable for use.
There were no significant physical property differences between the samples using in-house (blue) repro and those using commercial (clear) repro. However, the samples made with the commercial repro had a large number of “unmelts.” These are physical defects in the film due to small pieces of plastic (~10 to 100 μm) that are visible in the film and create a rough feel to the surface. Unmelts may be caused by contamination in the resin, often from higher melting plastic contaminants in the reprocessing feed stream.
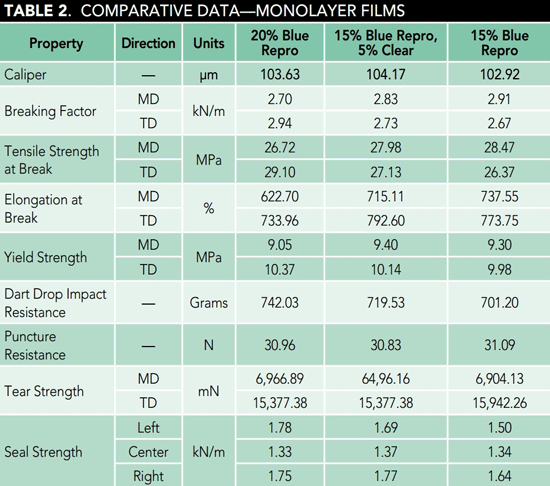
Table 2 shows results for a similar experiment run on a larger film line, with a die 20 in (500 mm) in diameter. The table compares films with 15 to 20% repro, in various combinations. Again, there were no significant differences between the physical properties at 15% or 20% repro, or with in-house vs. commercial repro. Again, however, the film made with commercial repro showed a large number of unmelts.
Coextruded Films
The films compared in Table 3 were produced on a machine with a 400-mm diameter die, with a blow up ratio of 2:1. The repro is used at 40% in the center layer, which makes up 50% of the film structure, so the repro makes up 20% of the bulk film composition. Here again, the differences between physical properties of the films are mostly not significant, with the possible exception of cross direction (CD) tear strength. The sample with all in-house repro appears to have somewhat better properties than the one made with commercial repro. The commercial repro used in this study was from a different source than the material used in the monolayer films. In the coextruded films, there was no significant increase in unmelts in films made with the commercial repro.
The data in Table 4 show an experiment with a different grade of film. This uses only 10% repro in the center layer (5% of film). It again shows no significant degradation of film physical properties.
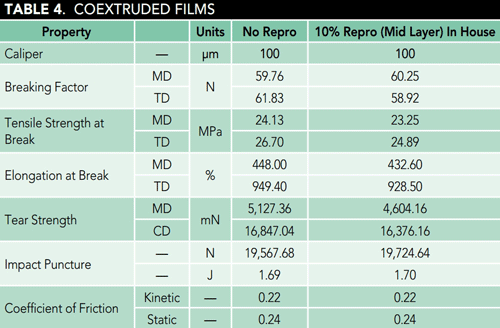
Conclusions
It is shown by the data presented in this article that it is feasible to make VCI packaging films using repro resins with no or minimal compromises in physical properties. Films containing up to 20% repro were demonstrated. In-house produced repro is generally superior due to its contribution of VCI to the final product, along with better consistency and generally reduced levels of contamination. From a cost perspective, commercial repro is generally about half the price of virgin resin. In-house repro can be significantly lower in cost, depending on the specific equipment used and local labor costs.
One further advantage of in-house reprocessing is the elimination of shipping; either one-way (purchase of commercial repro) or two-way (shipping scrap to the preprocessor and the return transit of the repro to the film facility). This produces significant environmental advantages in addition to the cost savings. The structure of coextruded films makes them especially well suited for incorporation of repro, as it can be “buried” in the middle layer with even less effect on bulk physical properties and VCI performance. Depending on the quality of in-house repro, it is likely that loading levels significantly greater than 20% can be achieved with good processability and film performance.
Acknowledgements
The authors thank Tim Bliss, Stephanie Berg, Snježana Mikolić, and Ivana Radić Boršić for data and assistance in preparing this article.
References
1 B. Miksic, R. Boyle, B. Wuertz, NACE International 2004 F.N. Speller Award Lecture: “Efficacy of Vapor Phase Corrosion Inhibitor Technology in Manufacturing,” Corrosion 60, 6 (2004): pp. 515-522.
2 V.A. Goldade, L.S. Pinchuk, A.V. Makarevich, V.N. Kestelman, “Films Incorporating Corrosion Inhibitors,” Plastics for Corrosion Inhibition (2005): pp 81-173.
3 S.M. Al-Salem, P. Lettieri, J. Baeyens, “Recycling and Recovery Routes of Plastic Solid Waste (PSW): A Review,” Waste Management 29, 10 (2009): pp. 2625-2643.
4. F. Vilaplana, S. Karlsson, “Quality Concepts for the Improved Use of Recycled Polymeric Materials: A Review,” Macromol. Mater. Eng. 293, 4 (2008): pp. 274-297.
5 ASTM D6988, “Standard Guide for Determination of Thickness of Plastic Film Test Specimens” (West Conshohocken, PA: ASTM, 2013).
6 ASTM D822, “Standard Test Method for Tensile Properties of Thin Plastic Sheeting” (West Conshohocken, PA: ASTM, 2002).
7 ASTM D1709, “Standard Test Methods for Impact Resistance of Plastic Film by the Free-Falling Dary Method” (West Conshohocken, PA: ASTM, 2004).
8 ASTM D1922, “Standard Test Method for Propagation Tear Resistance of Plastic Film and Thin Sheeting by Pendulum Method” (West Conshohocken, PA: ASTM, 2006).
9 ASTM D1894, “Standard Test Method for Static and Kinetic Coefficients of Friction of Plastic Film and Sheeting” (West Conshohocken, PA: ASTM, 2014).
10 ASTM F88, “Standard Test Method for Seal Strength of Flexible Barrier Materials” (West Conshohocken, PA: ASTM, 1999).
11 MIL-STD-3010, Test Method 2065, “Puncture Resistance” (Washington, DC: U.S. Dept. of Defense, 2002).
12 R.M. Patel, T.I. Butler, K.L. Walton, G.W. Knight, “Investigation of Processing-Structure-Properties Relationships in Polyethylene Blown Films,” Polym. Eng. Sci. 34 (1994): pp. 1506-1514.
13 K. Gillette, B. Berg, M. Kharshan, “Modern Advances in Environmentally Friendly Vapor-Phase Corrosion Inhibiting Coatings: Expanding the Realm of VPCI Packaging,” CORROSION 2009, paper no. 09486 (Houston, TX: NACE International, 2009), p. 14.
This article is based on CORROSION 2016 paper no. 7283, presented in Vancouver, British Columbia, Canada.