Cavitation is one of the most prevalent destructive phenomena in water pumps and valves. To help with oil extraction on Iranian oil platforms located in the Persian Gulf, high-capacity water pumps are used for injecting seawater into oil wells. Cavitation is the main cause for vibration, noise, reduced output capacity, and early pump failures. According to the laws of thermodynamics and fluid mechanics, cavitation is related to fluid velocity, local static pressure, and fluid temperature. This article explores possible remedies, including finishing the surfaces of pump components with a hydrophobic composite coating with a smooth and glassy surface, and the effect on the kinetics of cavitation bubble formation.
In the Persian Gulf, high-capacity pumps are used for injecting seawater into oil wells. The pumps are very important on offshore platforms for extracting oil, and they can be considered the heart of the platform. According to Figure 1, cavitation causes severe damage to the pumps, resulting in their failure in a short time (about one month).
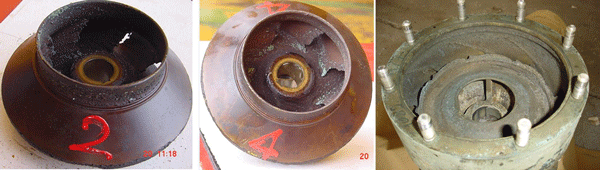
Thermodynamically, when local static pressure in seawater is less than the vapor pressure of seawater at a specific temperature, cavitation bubbles can be formed, which is actually the boiling of seawater by lowering pressure in the ambient temperature. Based on Bernoulli’s equation,1 when fluid velocity increases, its pressure decreases. Generally, this phenomenon occurs in piping system components such as pumps and valves. In a pump system, when the velocity of seawater rises above a critical value, the local static pressure of seawater in the pump becomes less than the vapor pressure of seawater; and seawater begins to boil. Thermodynamically, this condition can lead to the formation of cold cavitation bubbles.
The lifetime of the bubbles is short, and they collapse after reaching higher pressure areas. The collapse pressure is high enough (on the order of thousands of atmospheres) to cause noise, destroy the surfaces of the impeller and casing, and finally result in failure of the pump in a very short time.
Solutions Used
Based on the principles of thermodynamics and fluid mechanics, the following methods are typically recommended for controlling cavitation in pumps.2
• Develop an appropriate design to prevent an excessively high velocity of seawater in the pump, thus preventing low local pressure areas.
• Increase the total static pressure of the pump.
• Decrease the operating temperature.
In terms of production at oil platforms, it isn’t possible, in many cases, to implement all of the above recommendations, so other inhibiting factors must be applied. These require attention to nucleation and surface free energy, which can deter formation of the bubbles, and are related to kinetics of bubble formation.
According to Equation (1):

where ∆G = total free energy,
∆Gv = volume free energy (or thermodynamic free energy),
∆Gs = surface free energy, and R = radius of the nucleus, total free energy of the bubble nucleus is equal to the summation of its volume and surface free energy.3-5
When local static pressure is less than the vapor pressure of seawater,
∆v is negative but
∆s is positive. If
∆G becomes negative, then the nucleus can grow. Conversely, if
∆G becomes positive, then the nucleus will disappear and there is no cavitation condition. With decreasing pressure,
∆Gv becomes more negative and at a pressure that is much lower than the thermodynamic vapor pressure of seawater;
∆G then becomes negative, and the nucleus can grow to create a cavitation condition.
The bubble nucleation can be heterogeneous or homogeneous. In the heterogeneous condition, the nucleus forms on the surface of solid suspended particles in water or on the rough surfaces of the pump impeller and casing. In this case, some parts of the surfaces of the bubble nucleation are on the surfaces of the pump and solid particles; so the shape of the nucleus is not a perfect sphere and has a much lower force for nucleation than the perfect sphere shape.
In homogeneous nucleation, the nucleus must form without the help of foreign surfaces. This involves much greater opposite forces, and its nucleation requires much lower local static pressure compared to heterogeneous nucleation.
Managing conditions that lead to homogeneous nucleation in seawater pumps can be very difficult or impossible, but it is possible to move toward it. Preventing the entry of suspended solid particles into the pump and applying a polymer composite coating that has a very smooth and glassy surface are two additional methods for controlling cavitation.
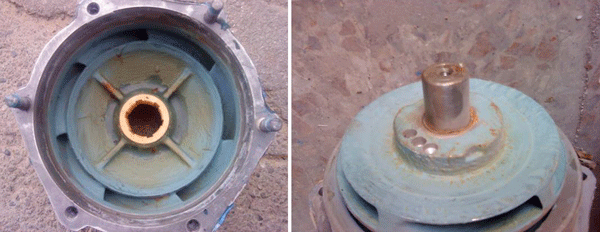
Figure 2 shows a pump that was coated with the polymer composite and in operation for 18 months at one Iranian Persian Gulf platform. In this pump, there were no cavitation defects on its surface coating. It seems that cavitation had not occurred on the coated surfaces of the impeller and casing. Cavitation had not concentrated on the surfaces of the pump because those surfaces were very smooth and, therefore, unsuitable for the nucleation of cavitation bubbles.
As shown in Figure 3, there are three conditions for the pump/seawater interface. In Figures 3(a) and (b), the pump surfaces are not coated and cavitation bubbles can form. In Figure 3(c), pump surfaces are covered by the polymer composite coating, which fills cavities and forms a hydrophobic surface.
The hydrophobic coating can prevent the nucleation of cavitation bubbles on surfaces.6 The bonding force of water molecules to the coating is higher than the bonding force of the bubbles’ gas molecules (i.e., the water/coating interface has lower surface free energy than the gas/coating interface). Therefore, the water/coating interface has greater stability than the gas/coating interface. As shown in Figure 3(c), the bubbles minimize the interface with the coating by forming nearly sphere-shaped bubbles, which are somewhat similar to spherical homogeneous bubbles.
Nucleation on coated surfaces had been moved toward homogeneous nucleation. Thus, nucleation on coated surfaces had become very difficult; and its concentration had been moved from the coated surfaces to other places in the seawater.
Before applying the coating to stainless steel impellers, chemical surface preparation was achieved by a mixture containing 14 kg oxalic acid (H2C2O4) and 12.2 kg concentrated sulfuric acid (H2SO4) (specific gravity 1.82) in 70 L of water at 85 °C. For brass impellers, only grit-blasting was used before applying the coating.
Conclusions
Sometimes the working conditions of offshore oil platforms cause cavitation to occur in large water injection pumps. This phenomenon has severe destructive effects on the pump, causing failure after a short time. Smoothing impeller and casing surfaces by applying a hydrophobic polymer composite coating is a good method for minimizing cavitation on the surfaces of injection seawater pumps of oil offshore platforms.
Acknowledgment
The assistance of M. Shirani, scientific member of Material and Structure Group at the Subsea R&D Center at Isfahan University of Technology, is greatly acknowledged.
References
1 “Bernoulli’s Equation,” https://www.grc.nasa.gov/www/k-12/airplane/bern.html (March 18, 2016).
2 C.E. Brennen, “Hydrodynamics of Pumps,” California Institute of Technology Pasadena, 2003.
3 M. Blander, J.L. Katz, “Bubble Nucleation in Liquids,” AIChE J. 21 (1975): pp. 833-848.
4 K.A. Morch, “Cavitation Nuclei and Bubble Formation” Dynamic Liquid-Solid Interface Problem, J. Fluids Eng. 122, 3 (2000): pp. 494-498.
5 A.C. Lawrence, “Nucleation and Stabilization of Microbubbles in Liquids,” Applied Scientific Research 38 (1982): pp. 101-115.
6 F. Liua, et al., “The Cavitation Erosion of the 45# Carbon Steels Implanted with Titanium and Nitrogen,” Tribology Transactions 35 (2010): pp. 239-243.