Project developers faced an unexpected challenge during the construction of a new natural gas plant (Figure 1) in Colorado in late 2014.
After 56 days of construction, the concrete in 20 circular columns supporting one of the plant’s control buildings had yet
to achieve its planned design strength of 4,000 psi (27.6 MPa). Because the control equipment was scheduled for installation in the building, the project’s construction team needed a solution that could be implemented as quickly as possible to strengthen those columns.
Each column had a diameter of 30 in (762 mm) and was built with cast-in-place construction.
Based on cylinder testing, the concrete had only reached a compression strength of about 2,000 psi (13.8 MPa) after those 56 days. The project engineer reanalyzed the structure and determined that the columns were still capable of supporting the loads, but with a lower margin of safety. The engineer wanted to protect and confine the columns to reduce the risks of any future spalling that might result from damage due to freeze-thaw or impacts during plant operations. The engineer was familiar with the line of Pipe Wrap products from Milliken Infrastructure Solutions (MIS) used to strengthen steel pipes and felt these products could be a good solution for the concrete columns (Figure 2).
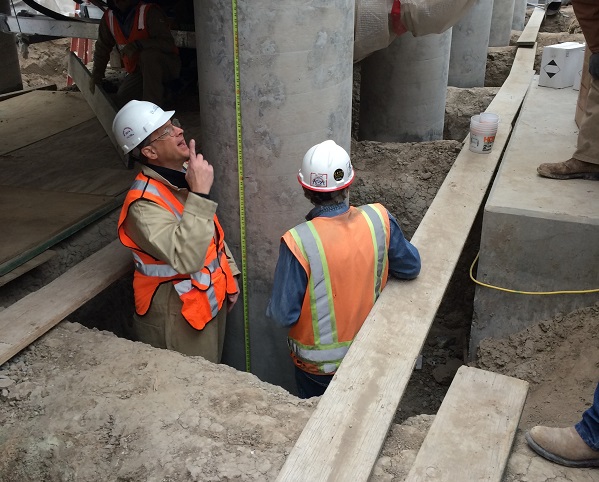
The companies quickly determined that the most suitable product to protect and strengthen the columns was the carbon fiber-reinforced polymer (FRP) strengthening system, which Gregg Blaszak, business development manager at Spartanburg, South Carolina-based MIS, describes as an externally bonded FRP made of carbon/epoxy used primarily for strengthening concrete structures. The FRP has a thickness of 0.05 in (1.27 mm) per layer, and it is virtually impermeable for this particular application.
“FRP turned out to be a simple and low-cost method,” says Blaszak. “Alternately, the contractor could have jacketed the columns with additional concrete to achieve the same objective, but that approach would have taken much longer to implement.”
For the Colorado plant, the company offered a solution of three layers of FRP to present to the engineer.
“Wrapping the deficient columns with three layers of carbon fiber would not only protect the concrete columns, but also provide the additional confinement to restore the column’s compression strength to nearly 4,000 psi [27.6 MPa],” Blaszak explains.
“It’s similar to how a steel cylinder confines the oil in a hydraulic jack,” he adds.
The application was “contact-critical,” which means that for the strengthened column to perform as intended, the FRP needed to be in contact with the surface of the concrete. The FRP did not need to be bonded to the concrete, just to itself. The columns were ground smooth, and the larger holes and voids were filled with epoxy paste.
Each of the three layers was applied separately and consecutively, with the material installed using wet lay-up techniques. The goal of wet lay-up was to completely saturate or impregnate the dry carbon fabrics with epoxy resin. While there are various ways to achieve this, for this application the dry fabric was pre-cut to the lengths required and then wet with two-part epoxy resin. This was done by distributing the resin across the fabric with a combination of rollers and squeegees and then working it into the dry fabric. The presaturated fabric was then applied directly to the columns. As an added benefit, the FRP serves as a waterproofing membrane that helps to reduce and slow the onset of any corrosion.
In the Colorado case, the installation of the wrap was planned over a two-week period in November to avoid impacting the overall construction schedule. The construction team began by excavating about 3 to 4 ft (1 to 1.2 m) around the perimeter of the columns to the footings, thus exposing the concrete to be wrapped.
Unfortunately, at that point a winter storm—with snow and winds in excess of 40 mph (64.4 km/h)—descended on the project site. Thankfully, the construction team had anticipated this weather beforehand and built temporary tenting around the exposed columns. The team also pumped in propane heat to elevate temperatures in the work area to 60 °F (15.5 °C) and kept backup heaters on standby. This was a critical component of the process, since the failure of any one heater would have compromised the FRP installation.
“Ideally, we would like to apply the product at closer to 70 °F (21 °C) to allow the resin to cure quicker,” Blaszak says. “However, heating the storage space prior to application allowed the carbon fiber to achieve the desired strength.”
“We provided confinement by wrapping, which resulted in both additional axial strength and protection,” he adds. “The contractor did an outstanding job under some of the most extreme conditions I have seen.”
The wrap was then covered with a UV-resistant coating (Figure 3), and the contractor put fine sand onto the wet epoxy of the final layer to promote adhesion of the paint.
The service life of the wrap (Figure 4) is significant, and Blaszak notes that FRP projects have been in service for more than 30 years with no apparent problems. Although FRP was a successful solution in the Colorado case, project officials say it should primarily be used within a broader repair strategy.
“It is essential to address the sources of the deterioration or deficiencies as part of an overall repair strategy prior to applying the FRP,” Blaszak says. “It is only as good as the substrate it is bonded to.”
Source: Milliken Infrastructure Solutions, Web site: http://infrastructure.milliken.com/renewwrap-strengthening-system.