Paint selection for bridge application is no simple task. When the need arose in 1991 for painting the Piscataqua River Bridge (Figures 1 and 2), which connects Portsmouth, New Hampshire, USA with Kittery, Maine, USA, it spurred the New Hampshire Department of Transportation (NHDOT) to find a solution.
The Northeast Protective Coating Committee (NEPCOAT) (Figure 3) was not yet in existence, hence the only option for assistance regarding coating selection was the Michigan Department of Transportation, which offered an “Approved Paint List.”
Complications surrounding paint selection included the Federal Highway Administration (Washington, DC, USA) eliminating the use of paint containing lead, the transitioning from alkyd paint systems to zinc/epoxy/urethane three-coat systems, the lowering of volatile organic compound (VOC) limits, plus the release of the Occupational Safety and Health (Washington, DC, USA) standard, “Lead in Construction.”
So, what can be done when lead paint is not an option? What about when VOC limits are lowered? Or when new paint systems are created? How is a coating chosen when that coating is required to work for dozens of years? In his 2022 AMPP conference paper on which this article is based, Jerry S. Zoller explores how NEPCOAT came into being and how it has evolved over the years—from publishing a “Qualified Products List” (QPL) to performing lab testing.1

NEPCOAT was formed in 1992 based on the need to evaluate and qualify paint systems to identify the best performers. It is made up of ten different Departments of Transportation—Connecticut, Delaware, Massachusetts, Maine, New Hampshire, New Jersey, New York, Pennsylvania, Rhode Island, and Vermont. For the past 30 years they have worked to evaluate paint for bridge applications and have biannually published the previously mentioned QPL. By 2001, they had tested 45 paint systems and approved 20 of them for use.
From 1997 to 2001, there was significant cooperation between NEPCOAT and the American Association of State Highway and Transportation Official (AASHTO) (Washington, DC, USA). It was during this time that AASHTO adopted NEPCOAT’s specification, made improvements to it, and put it through an approval process. Final acceptance on the specification, now referred to as R-31, was completed in 2002.
Furthermore, AASHTO implemented the National Transportation Product Evaluation Program (NTPEP), which included lab testing. AASHTO manages the testing, coating submissions, payments, and dissemination of test results of the NTPEP.
In 2003, AASHTO introduced an online test results storage platform called DataMine. The public and DOTs have access to this information.
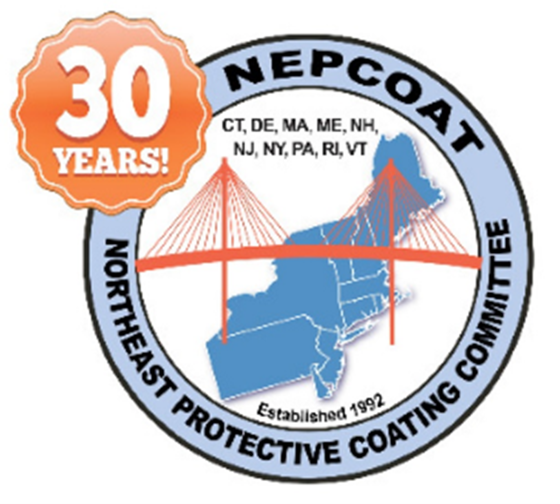
Although NEPCOAT no longer oversees the testing (as of 1991), they do review and accept test data on DataMine. Additionally, they produce acceptance criteria and continue to publish the QPL.
For a coating system to be accepted by the original NEPCOAT standard as well as R-31, it must pass seven different lab tests. R-31 also is considering an additional eighth test. These lab tests are described in further detail in the following paragraphs.
1. Slip coefficient:
This test, along with the companion tension creep test, assures structural integrity at bolted connections on a bridge. To guarantee bolted plates will not slip, contact steel surfaces must be painted to defend against rust inside those bolted connections.
In the slip coefficient test, three plates are bolted and clamped together, then a compression force is applied until the center plate slips.
In the tension creep test, three sets of clamped plates are loaded by force and monitoring instruments can detect any slippage that may occur.
2. Salt fog resistance:
In this test, steel panels are subjected to a constant mist of sodium chloride (NaCl) spray at a high temperature.
3. Cyclic weathering:
By using two cabinets, one to test ultraviolet (UV) light and the other to test salt fog, this test simulates weather conditions. Panels are first placed in the UV cabinet for seven days and undergo 4 h of UV exposure at 140 °F, followed by 4 h of water condensation at 77 °F.
Next, they are moved to the second cabinet where they endure cycles of salt fog at ambient temperature for 1 h, followed by a dry cycle at 95 °F.
4. Abrasion resistance:
The objective of this test was to measure durability and toughness of paint exposed to a rotating abrasion wheel. This test was performed years ago, but has since been found to be ineffective and has been stopped.
5. Adhesion:
Four pull stubs are glued to each panel, then pulled off with an adhesion tester. Doing so allows the amount of adhesion between the coating and panel to be measured. Researchers perform this test on panels coated with primer only and with the full system.
6. Freeze/thaw adhesion:
Panels are subjected to a freeze/thaw cycle for 30 days. Three cycles occur every 24 h—16 h at -22 °F, 4 h at 122 °F, and 4 h of immersion in water at 77 °F. Following the test, pull-off adhesion tests and results are compared with results from the original adhesion test to evaluate whether the paint system continues to meet the minimum required adhesion value.
7. Coating identification:
Over 25 properties are tested for in each submitted paint sample. The purpose is to compare against manufacturer’s claims, as well as ensure governmental compliance.
8. Two-year atmospheric exposure:
This test is only a part of the R-31 specification. It involves placing test panels near the Atlantic Ocean; however, has yet to be implemented.
Zoller emphasizes that AASHTO NTPEP lab testing to determine the effectiveness of bridge paint systems “has become the backbone and source of independent and reliable information upon which owners of steel highway bridges can make informed decisions regarding coating selection for totally cleaned steel, either in the shop or in the field.”1
NEPCOAT’s continuous work evaluating lab data and growing their reach from the regional to national level has proven invaluable. In fact, half of U.S. state’s DOTs use NEPCOAT’s QPL.
By continuing to evaluate lab data uploaded to DataMine, develop acceptance criteria, and publish a QPL, NEPCOAT disseminates important and helpful information that allows users to make informed decisions regarding paint for use on bridges.
Reference
1 J.S. Zoller, “The NEPCOAT Story-Bridge Paint Selection in the Northeast,” AMPP 2022, paper no. 17834 (Houston, TX: AMPP, 2022).
Editor’s note: This article is repurposed from the October 2022 print issue of Materials Performance (MP) Magazine.