Galvanizing has proven to be effective in providing corrosion protection for steel. Galvanized steel is commonly used in construction of refineries and chemical processing facilities. In fire risk areas, the galvanized steel must be fireproofed.
When steel is galvanized, the zinc coating becomes the foundation of the fireproofing system. The galvanized steel and fireproofing system must perform in unison while in service and, if necessary, during a fire. Factors within the galvanization and surface preparation process influence the system’s ability to perform.
Corrosion protection is the recognized value for galvanizing steel. Corrosion protection is achieved by cathodic protection. When the steel is exposed to moisture, the zinc sacrifices itself and forms a passivating layer over exposed bare steel adjacent to the zinc coating. This significantly reduces the rate of steel corrosion.
This electrochemical reaction continues until all the zinc has been depleted. Without moisture to complete the electrochemical circuit between the zinc coating and the bare steel, no oxidation occurs, resulting in no loss of the zinc coating.1 This is one of the primary reasons atmospherically exposed galvanized steel provides many years of corrosion protection,2 as surface moisture evaporates allowing the galvanized surface to dry.
The hot-dip batch galvanizing process consists of immersing steel into a series of tanks. Prior to galvanizing steel members, imperfections, such as weld spatter, sharp edges, and fins are removed. The first dipping process consists of immersing the steel into a caustic solution to remove grease, oil, waxes, and dust, along with any other contaminates that may be present. Following the caustic cleaning, the steel is immediately immersed into a rinsing tank.
Next, the steel is immersed into a pickling tank, which is typically a diluted hydrochloric acid solution. The purpose of pickling is to remove rust and scale. Given the various thicknesses of the scale layers, immersion time in the pickling tank varies. The steel is rinsed once again and then immersed into the flux solution, consisting of a zinc ammonium chloride solution with other additives. Fluxing activates the cleaned steel so that the galvanized zinc coating forms quickly.
The steel is then immersed into a molten zinc kettle. A metallurgical reaction takes place between the steel and the zinc, forming a zinc alloy coating. After being immersed into the molten zinc bath for the appropriate amount of time, it is removed and cooled to stop the metallurgical reaction process.
The amount of metallurgical reaction within the zinc coating impacts its physical properties. Galvanizing produces four distinct alloy layers within the zinc coating. The layers, beginning from the steel surface, are: gamma (75% Zn, 25% Fe), delta (90% Zn, 10% Fe), zeta (94% Zn, 6% Fe), and eta (100% Zn).2 These four layers produce varying levels of hardness.
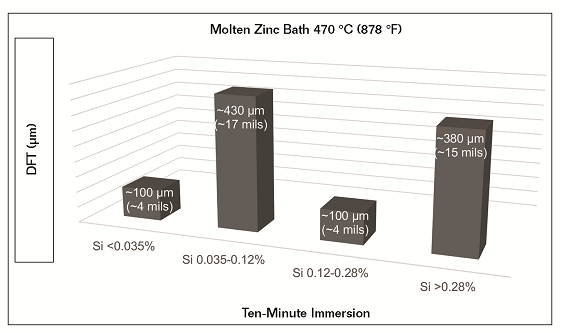
Using the diamond pyramid hardness (DPN) test method, the hardness of each zinc alloy layer is, starting with the steel: Fe (159 DPN), gamma (250 DPN), delta (244 DPN), zeta (179 DPN), and eta (70 DPN).3 DPN testing confirms that the alloy layers immediately adjacent to the steel are significantly harder than the steel substrate, therefore more rigid, and the pure zinc layer is 56% softer than the steel. The thickness of each layer within the zinc coating can vary according to several factors, such as: immersion time in the zinc bath, zinc bath temperature, the rate of cooling once removed from the molten zinc bath, surface roughness of the steel, and the amount of silicon and phosphorus within the steel.
Silicon is added to steel alloys to obtain required strength and hardness properties. Phosphorus is also used in conjunction with silicon for the same purpose, but typically at lower quantities. Laboratory testing and evaluation has proven that silicon and phosphorus, mostly silicon, have profound impacts on layer growth within the zinc coating and the speed of film build formation.4 Silicon accelerates layer growth. In order to control the layer growth and the thickness of the zinc coating, galvanizers must ensure that the zinc bath temperature be within a defined temperature range, according to the percent of silicon stated on the certified mill test report. At times, this has proven to be problematic.5
Silicon and phosphorus are not always evenly distributed throughout the steel.6 Depending on when and where the mill test sample was taken, the certified report may not be representative of the actual steel being galvanized.7 Coating thickness, within the same immersion time, greatly varies with changes in zinc bath temperature and silicon content. Using test data results,4 Figure 1 illustrates the effects that silicon content has on total coating thickness achieved in a zinc bath of 470 °C (878 °F) after ten minutes of immersion.
The risk of experiencing a failure increases as zinc film build increases, approximately 305 µm (12 mils) dry film thickness (DFT) and higher.8 Controlling the metallurgical reaction in the zinc coating and achieving a desired film build can be challenging for galvanizers. In addition to silicon and phosphorus, the surface profile of steel impacts layer growth and film build. If the steel is abrasive blasted, it increases the unit area that reacts with the molten zinc, resulting in layer growth at multiple angles from the surface of the steel.
The amount of layer growth within the zinc coating and the actual DFT obtained are influenced by the actual steel member’s alloy composition, its surface roughness, and its relationship to the actual galvanizing parameters: efficiency of the surface preparation process, molten zinc bath composition, zinc bath temperature, immersion time, and the rate in which the steel cools.4 Alterations, in any of the given variables, produce a zinc coating with different layer growth properties at a different DFT.
Galvanizing may fail as a result of too much film build and/or layer growth. As hardness tests confirm, the zinc alloy layers within the galvanizing film are significantly harder than the steel and outer pure zinc layer. Layer growth increases hardness and thereby reduces its flexural properties. Fireproofed galvanized steel members must withstand flexing during transportation and construction.
Also, the coefficient of thermal expansion (CTE) properties can significantly vary, placing shear stress within the various layers: steel/galvanizing interface, within the various layers in the zinc coating, and at the galvanizing/fireproofing interface. Flexing, expansion, and contraction may lead to detachment within the zinc coating.4
Detachment of galvanizing is classified as either peeling or flaking, depending on the location within the zinc coating it loses adhesion.
Flaking occurs at the gamma layer at the surface of the steel.4 The galvanizing is completely removed, or only a trace is left on the steel (see Figures 2 and 3). The gamma layer is the most rigid layer and flaking may occur as a result of flexing or an external force being applied.4 Flaking can also occur in heat affected areas, such as edges, where thermal cutting techniques were used.9 Excessive heat alters the microstructure and properties of the steel, impacting the steel’s effectiveness to be galvanized.
Peeling occurs where the alloy layers transition to the pure zinc layer.4 This is a result of vacancies that developed during the reaction between the steel and zinc, most likely a result of prolonged cooling after being removed from the zinc bath and/or having a high film build, which takes longer to cool.4 Steel members must be designed to allow the molten zinc to flow off without accumulating, creating thick areas. Fireproofed galvanized steel, having areas with compromised bonding, typically become apparent within a year of being exposed to the full range of thermal cycles and having been in the actual operating conditions.
Guidelines and practices are provided within the industry specific to preparing galvanized steel for painting, such as ASTM D6386-16a “Standard Practice for Preparation of Zinc (Hot-Dip Galvanized) Coated Iron and Steel Product and Hardware Surfaces for Painting.”10 Industry guidelines specific for preparing galvanizing to be fireproofed appear nonexistent.
Epoxy intumescent coating materials place much more stress on galvanizing than conventional coating systems, having greater mass, high internal cross-linking tension within the dried film, and having a different CTE than that of the galvanized steel substrate. Therefore, it is imperative that the galvanizing be: well bonded to the steel, structurally sound, have a proper surface profile, and free from surface contamination.
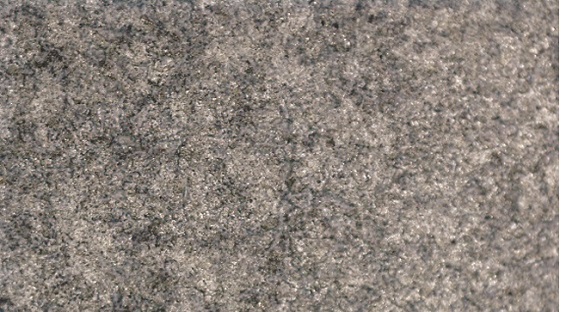
An optimum angular profile for epoxy intumescent coatings on bare steel ranges between 50 to 75 µm (2 to 3 mils), with an approximate peak count between 35 to 47 peaks per linear centimeter (90 to 120 peaks per linear inch). The texture of galvanized finishes greatly varies, even on the same steel member.
As Figure 4 illustrates, the natural texture of galvanizing is mostly nodular, not angular, with a typical profile height ranging from 50 to 90 µm (2 to 3.5 mils). Several contributing factors influence the texture of galvanizing, such as: initial steel profile, silicon and phosphorus content, dross and other particles in the zinc bath, and uneven flow of the zinc off the steel.8 The natural finish of galvanizing must be sweep blasted, using low pressure,11 to achieve an angular profile within the optimum peak count range.
The objective of blasting is to create an angular profile over the natural texture and without removing more than 50 µm (1 mil) of the zinc coating.10 In order to do so, industry guidelines, such as those described in section 5.4.1 of ASTM D6386-16a, must be followed.
A proper angular profile must be achieved and confirmed. Given the inconsistency of the natural galvanized finish, using a portable stylus instrument, per ASTM D7127-17 “Standard Test Method for Measurement of Surface Roughness of Abrasive Blast Cleaned Metal Surfaces Using Stylus Instrument,” has proven to be beneficial. Data produced within the linear measurement includes: peak/valley pair counts, vertical distance between highest peak and lowest valley, along with other useful data. It is important to be aware that profile inspection instruments do not confirm whether the profile is nodular or angular. Therefore, it is imperative that galvanized surfaces be thoroughly abrasive blasted according to standard.
Passivating treatments on galvanizing compromise adhesion. The blasted galvanized surface must be verified as being free from passivating treatments, according to surface preparation specification SSPC-SP 16 “Brush-Off Blast Cleaning of Coated and Uncoated Galvanized Steel, Stainless Steels, and Non-Ferrous Metals,” section 4.3.3. Fireproofing coating systems applied over galvanized steel, containing passivators, will likely detach from the surface after being exposed to low thermal cycles, during expansion and contraction, as shown in Figure 5.
Galvanizing should be sealed with a primer immediately following inspection. Zinc reacts instantly with the environment, first forming zinc oxide on the surface.10 Also, hydrogen can be absorbed into the steel during the pickling process. Hydrogen effusion from the steel, during the molten zinc state, can form pores or blisters within the zinc coating.4 After being abrasive blasted, these small openings near the surface are exposed.
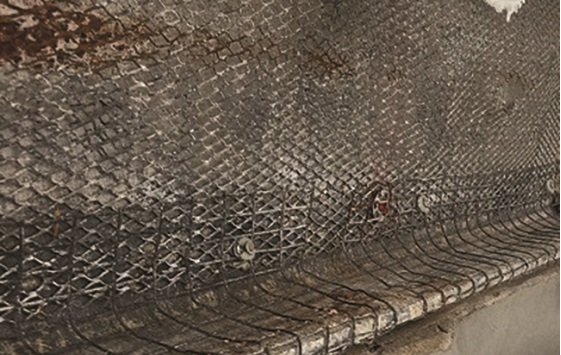
Epoxy primers, with good wetting properties, should be used to wet out any zinc oxide present and to penetrate through all porous areas that may exist within the galvanizing. Primers used under fireproofing must be tested and approved by the fireproofing manufacturer to ensure it is compatible, including those used for repairs at the galvanizing facility.
Dense and proprietary Portland-based lightweight cementitious fireproofing fuels zinc consumption. The porosity of these materials, along with cracks that may be present, allows moisture to access the galvanized steel. Moisture is absorbed and retained. The retained moisture, commonly being acidic and or containing chlorides, effectively maintains the electrochemical circuit, or corrosion cell. This is made evident by rust bleed through the cement, corroded galvanized reinforcement, and corrosion on the steel structure. Figure 6 illustrates depleted zinc and corrosion occurring within four years of exposure.
Zinc’s thermal properties could lead to premature failure, while in service or during a fire. Two temperature ranges may prove to be detrimental to galvanizing: ~200 °C (390 °F) and higher,12 and 420 °C (788 °F). Exposure around 200 °C (390 °F)13 may result in an adverse metallurgical reaction producing gaps within the galvanizing, leading to detachment. At 419 °C (787 °F),14 zinc reaches its melting point.
Often, the limiting temperature for onshore fire protection within hydrocarbon processing plants is 538 °C (1000 °F), such as with specifications requiring UL 1709 certifications over bare steel. To ensure proper fire protection of galvanized steel, fireproofing certifications over galvanizing should be used, or certified DFTs proven to insulate the steel below the melting point of zinc. Otherwise, the required fire rating may be compromised.
Conclusion
Given the inherent challenges discussed, close evaluations must be conducted throughout the galvanizing and surface preparation process. It is imperative that the galvanizing be: well bonded to the steel, structurally sound, and properly prepared prior to fireproofing. Fireproofing serves a critical role in mitigating fire damage, providing safety to personnel, and preventing harmful environmental impacts. Therefore, being able to recognize potential issues and being aware of the surface preparation methods required aids in reducing the risk of a premature failure.
References
1 P.R. Roberge, Corrosion Basics: An Introduction, 3rd ed. (Houston, TX: NACE International, 2018), pp. 31-32, 97-105, 328, 549.
2 C.G. Munger, L.D. Vincent, Corrosion Prevention by Protective Coatings, 3rd ed. (Houston, TX: NACE, 2014), pp. 127-128.
3 “Galvanized Coating Layers,” Construction Canada, May 27, 2019, https://www.constructioncanada.net/harness-design-freedomwith-hot-dip-galvanized-steel/galvanized_coating_layers_2016_english (October 26, 2019).
4 P. Maaß, P. Peißker, eds., Handbook of Hot-Dip Galvanization (Weinheim, Germany: Wiley-VCH, 2011), pp. 94-116, 410-414.
5 D. Barlow, “Possible Inaccuracies of the Mill Test Report,” American Galvanizers Association, March 4, 2014, https://galvanizeit.org/knowledgebase/article/possible-inaccuracies-of-the-mill-test-report (October 25, 2019).
6 B.A. Duran III, “Rough Galvanized Coatings,” American Galvanizers Association, May 1, 2009, https://galvanizeit.org/knowledgebase/article/rough-galvanized-coatings (October 25, 2019).
7 B.A. Duran III, “Silicon Content of Steel,” American Galvanizers Association, August 30, 2012, https://galvanizeit.org/knowledgebase/article/silicon-content-of-steel (October 25, 2019).
8. “Inspection of Hot-Dip Galvanized Steel Products” (Centennial, Colorado: American Galvanizers Association, 2016): pp. 9-17.
9 A. Fossa, “Prevent Thin and/or Flaking Coatings from Thermally Cut Edges,” American Galvanizers Association, https://galvanizeit.org/knowledgebase/article/prevent-thin-and-or-flaking-coatings-from-thermally-cut-edges (April 6, 2016).
10 ASTM D6386-16a, “Standard Practice for Preparation of Zinc (Hot-Dip Galvanized) Coated Iron and Steel Product and Hardware Surfaces for Painting” (West Conshohocken, PA: ASTM International, 2016), pp. 2-3.
11 “Guide to Preparing Hot-Dip Galvanized Steel for Paint” (Centennial, Colorado: American Galvanizers Association, 2011).
12 ASTM D7127, "Standard Test Method for Measurement of Surface Roughness of Abrasive Blast Cleaned Metal Surfaces Using Stylus Instrument" (West Conshohocken, PA: ASTM).
13 SSPC-SP 16, "Brush-Off Blast Cleaning of Coated and Uncoated Galvanized Steel, Stainless Steels, and Non-Ferrous Metals" (Pittsburgh, PA: SSPC).
14 B.A. Duran III, “Galvanized Steels Performance in Extreme Temperatures,” American Galvanizers Association, April 3, 2013, https://galvanizeit.org/knowledgebase/article/galvanized-steel-s-performance-in-extreme-temperatures (October 25, 2019).
15 B.A. Duran III, “Sweep Blasting Galvanized Steel,” American Galvanizers Association, October 11, 2011, https://galvanizeit.org/knowledgebase/article/sweep-blasting-galvanized-steel (October 25, 2019).
16 J.E. Neely, Practical Metallurgy and Materials of Industry, 4th ed. (Upper Saddle River, New Jersey: Prentice Hall, Inc., 1994), p. 63.